Mastering The Five S: A Comprehensive Guide To Enhance Productivity And Efficiency
Discover the transformative power of the Five S methodology, a renowned system designed to streamline processes, enhance productivity, and create an organized work environment. This approach has been adopted by industries worldwide, proving its effectiveness in delivering measurable results. Whether you're a business owner, manager, or employee, understanding the Five S principles can significantly improve your workflow and operational efficiency.
The Five S methodology, originally developed in Japan, is a lean management tool that emphasizes organization, cleanliness, and standardization. It provides a structured approach to maintaining a workplace that promotes efficiency, safety, and employee satisfaction. By implementing these principles, organizations can reduce waste, minimize errors, and improve overall performance.
In this article, we will delve deep into the Five S concepts, exploring their origins, benefits, and practical applications. We'll also provide actionable tips and strategies to help you implement these principles effectively in your workplace. Let's embark on this journey to transform your work environment into a model of efficiency and productivity.
Read also:Unveiling The Timeless Appeal Of The 66 Camaro A Journey Through Automotive History
Table of Contents
- The Origin of Five S
- The Five S Principles
- Benefits of Implementing Five S
- How to Implement Five S
- Common Challenges and Solutions
- Tools and Resources for Five S
- Real-World Examples of Five S Success
- Five S vs. Other Lean Tools
- The Future of Five S in Modern Workplaces
- Conclusion and Call to Action
The Origin of Five S
The Five S methodology traces its roots back to Japan, where it was initially developed as part of the Toyota Production System (TPS). The concept was designed to create a clean, organized, and efficient workplace, which would ultimately lead to improved productivity and quality. Each "S" represents a specific principle, and together, they form a holistic approach to workplace management.
Historical Context
In post-war Japan, industries were under pressure to increase productivity and reduce costs. The Five S methodology emerged as a solution to these challenges, helping organizations achieve their goals by focusing on waste reduction and process optimization. Over time, the principles of Five S have been adapted and applied across various industries worldwide, proving their universal applicability.
The Five S Principles
At the core of the Five S methodology are five principles, each represented by an "S." These principles work together to create a systematic approach to workplace organization and efficiency.
Sort (Seiri)
The first principle, Sort, involves identifying and removing unnecessary items from the workplace. This step helps reduce clutter, minimize distractions, and create a more focused environment. By sorting items, organizations can improve safety, save time, and optimize space utilization.
Straighten (Seiton)
Straighten focuses on organizing essential items in a logical and accessible manner. This principle emphasizes the importance of having a place for everything and ensuring that everything is in its place. Proper organization reduces search time and enhances workflow efficiency.
Shine (Seiso)
Shine involves maintaining cleanliness and order in the workplace. Regular cleaning and maintenance not only improve the appearance of the workspace but also contribute to a healthier and safer environment. A clean workplace fosters a sense of pride and professionalism among employees.
Read also:Ninja Kids Net Worth The Rising Phenomenon Of Child Gaming Stars
Standardize (Seiketsu)
Standardize aims to establish consistent practices and procedures across the organization. By creating standardized processes, companies can ensure that everyone follows the same guidelines, reducing variability and improving overall performance. This principle promotes a culture of discipline and accountability.
Sustain (Shitsuke)
Sustain is the final principle, focusing on maintaining and continuously improving the Five S practices. This step involves embedding the principles into the organization's culture and ensuring long-term commitment. Sustaining the Five S methodology requires ongoing effort and dedication from all levels of the organization.
Benefits of Implementing Five S
Implementing the Five S methodology offers numerous benefits for organizations across various industries. From improving productivity to enhancing employee morale, the advantages of this approach are both tangible and intangible.
- Increased productivity through streamlined processes
- Reduced waste and improved resource utilization
- Enhanced safety and reduced risk of accidents
- Improved quality of products and services
- Boosted employee morale and job satisfaction
How to Implement Five S
Successfully implementing the Five S methodology requires a structured approach and active participation from all team members. Below are the key steps to follow when introducing Five S in your organization:
Step 1: Conduct a Workplace Assessment
Begin by evaluating your current workplace conditions. Identify areas that need improvement and prioritize them based on their impact on productivity and efficiency.
Step 2: Involve Employees in the Process
Engage your team in the implementation process to ensure buy-in and commitment. Encourage feedback and suggestions to create a sense of ownership and collaboration.
Step 3: Develop an Action Plan
Create a detailed plan outlining the steps required to implement each principle. Set clear goals and timelines to track progress and measure success.
Step 4: Monitor and Evaluate
Regularly monitor the implementation process and evaluate its effectiveness. Use key performance indicators (KPIs) to measure improvements and identify areas for further enhancement.
Common Challenges and Solutions
While the Five S methodology offers numerous benefits, its implementation can present challenges. Below are some common obstacles and solutions to overcome them:
- Resistance to Change: Address resistance by educating employees about the benefits of Five S and involving them in the process.
- Lack of Resources: Allocate necessary resources and prioritize areas that will yield the highest impact.
- Difficulty in Sustaining: Develop a plan to maintain Five S practices and incorporate them into the organization's culture.
Tools and Resources for Five S
Various tools and resources are available to support the implementation of the Five S methodology. These include visual aids, training materials, and software solutions designed to facilitate the process.
Visual Management Tools
Visual management tools, such as labels, signs, and color-coding systems, help organize the workplace and improve communication. These tools make it easier for employees to identify and locate items quickly.
Training Programs
Comprehensive training programs can educate employees about the Five S principles and provide them with the skills needed to implement them effectively. These programs often include workshops, seminars, and online courses.
Real-World Examples of Five S Success
Many organizations have successfully implemented the Five S methodology, achieving significant improvements in productivity and efficiency. Below are some notable examples:
- Toyota: As the pioneer of Five S, Toyota continues to benefit from its application in manufacturing processes.
- Hospitality Industry: Hotels and restaurants have adopted Five S to enhance cleanliness and improve guest satisfaction.
- Healthcare Sector: Hospitals use Five S to streamline operations and improve patient care.
Five S vs. Other Lean Tools
While the Five S methodology is a powerful tool for improving workplace efficiency, it is not the only lean management approach available. Comparing Five S with other tools, such as Kaizen and Six Sigma, can help organizations determine the best fit for their needs.
Kaizen
Kaizen focuses on continuous improvement through small, incremental changes. While both Five S and Kaizen aim to enhance efficiency, Kaizen places greater emphasis on employee involvement and innovation.
Six Sigma
Six Sigma is a data-driven approach to reducing defects and improving processes. Unlike Five S, which emphasizes organization and cleanliness, Six Sigma relies on statistical analysis to identify and eliminate variations.
The Future of Five S in Modern Workplaces
As workplaces continue to evolve, the Five S methodology remains relevant and adaptable to changing environments. With advancements in technology and increasing emphasis on sustainability, the principles of Five S can be expanded to address modern challenges.
Integration with Technology
Integrating Five S with digital tools and automation can enhance its effectiveness in modern workplaces. For example, using IoT devices to monitor workplace conditions or implementing AI-powered systems to optimize resource allocation can complement traditional Five S practices.
Conclusion and Call to Action
In conclusion, the Five S methodology offers a comprehensive approach to improving workplace efficiency and productivity. By implementing the principles of Sort, Straighten, Shine, Standardize, and Sustain, organizations can create a cleaner, safer, and more organized environment that fosters success.
We invite you to take action by exploring how the Five S methodology can benefit your organization. Share your thoughts and experiences in the comments section below, and don't forget to explore other articles on our site for more valuable insights into workplace management and productivity.
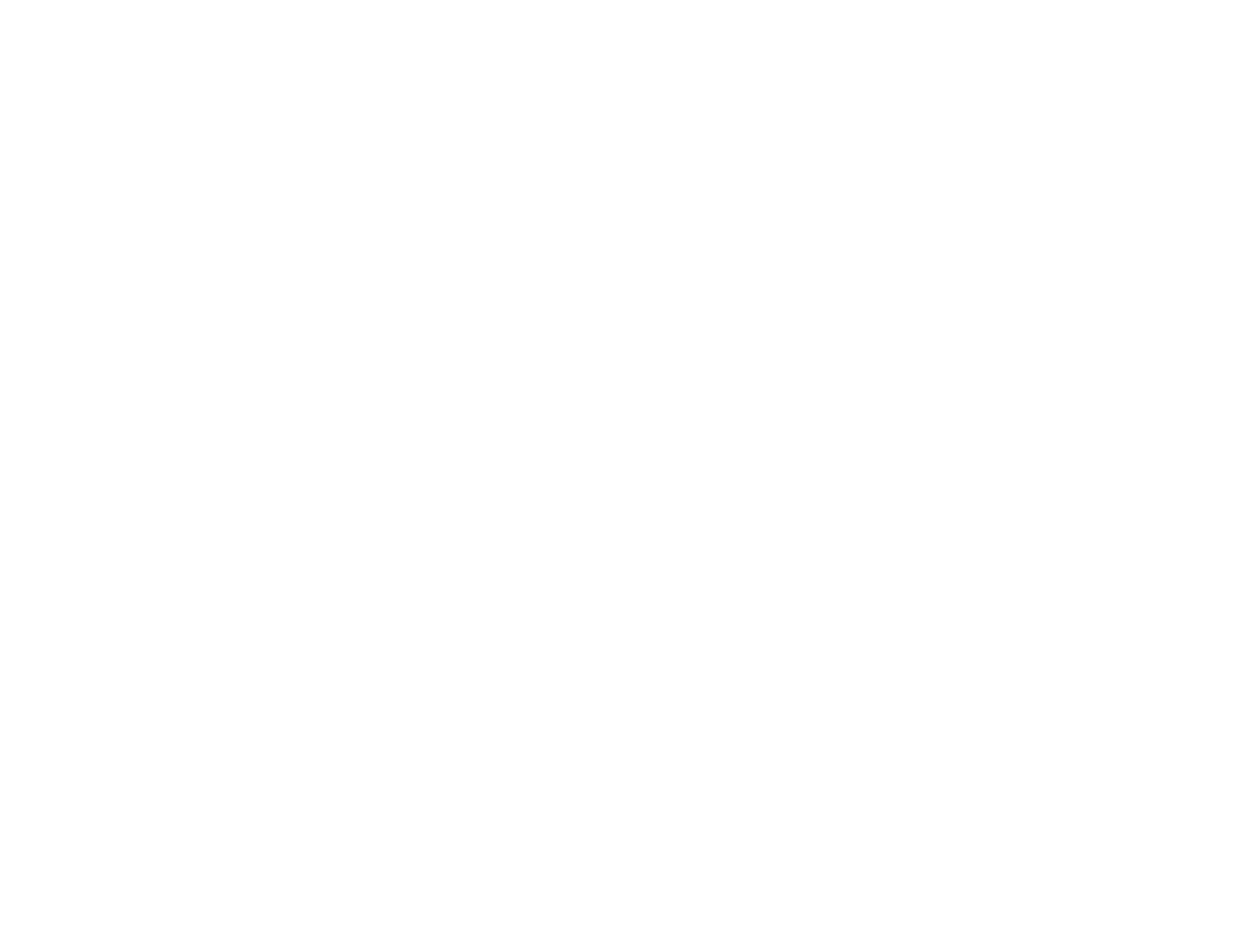
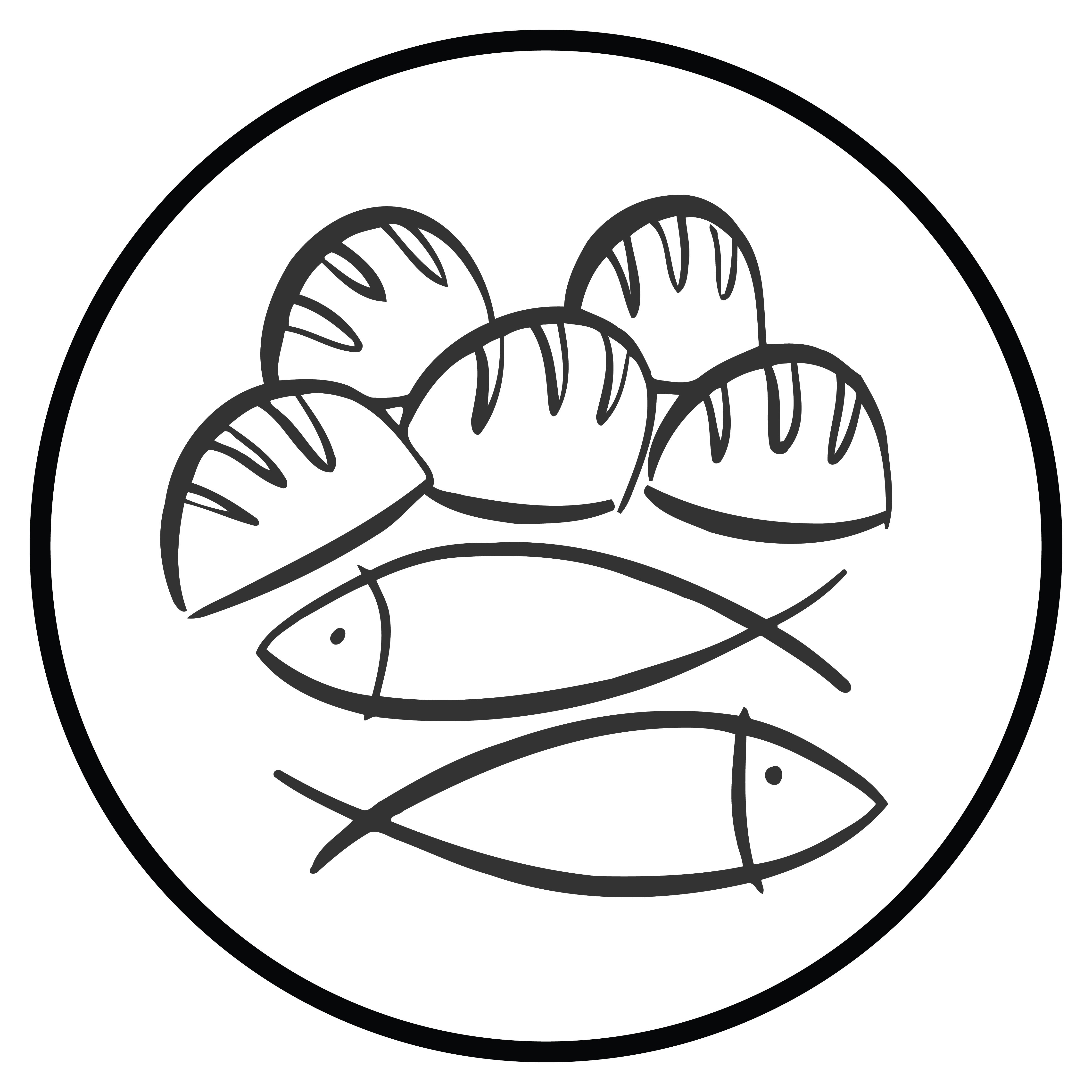